How Did the Polyurethane Molding Process Revolutionize the Electrical Industry?
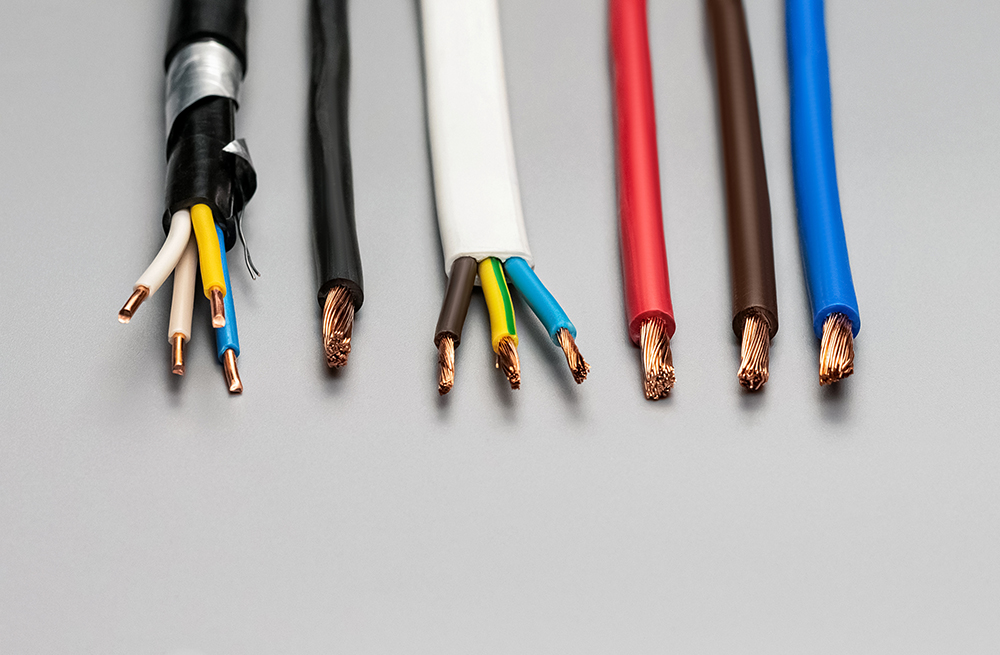
Are you tired of dealing with the limitations and frustrations of traditional molding processes in the electrical industry? The difficulties of working with molds that result in subpar electrical components—from air bubbles and shrinkage rates to limited durability and inconsistent physical properties—can be exasperating. These issues not only hinder production efficiency but also compromise your final products' overall performance and reliability.
In this blog post, we will delve into the impact of polyurethane molding on the electrical industry and how it can provide a superior solution to your current challenges. Through our expertise and cutting-edge polyurethane molding products, we will explore the incredible benefits that polyurethane molding brings to the electrical industry. Polyurethane molding offers unparalleled advantages over traditional molding methods, From its exceptional abrasion and chemical resistance to its ability to withstand extreme temperatures.
By choosing Stoner Molding Solutions, you will understand how polyurethane molding can transform your electrical manufacturing process. Our team of experts is ready to guide you every step of the way, providing solutions tailored to your specific needs. Don't let outdated processes hold you back any longer. Contact us today for assistance with your polyurethane molding process and unlock the full potential of your electrical components.
Why Is Polyurethane Molding So Popular in the Manufacturing Sector?
In the fast-paced world of manufacturing, efficiency and reliability are paramount. That's why polyurethane molding has become an increasingly popular choice for manufacturers across various industries, including electrical applications. The versatility and unique properties of polyurethane make it an ideal material for creating high-quality, durable components.
Polyurethane offers exceptional abrasion resistance, chemical resistance, and thermal expansion properties, making it well-suited for the demanding requirements of the manufacturing sector. Polyurethane molding delivers outstanding results, whether insulating components, protective covers, or intricate parts with sharp corners and complex geometries.
Stoner Molding Solutions understands the need for manufacturers to optimize their production processes and mold more parts in less time. With years of experience and a focus on industrial molding solutions, we have made polyurethane molding easier and faster. By partnering with us, manufacturers can access top-quality mold release agents specifically designed for industrial uses, ensuring smooth and efficient production cycles.
Why Is Polyurethane Ideal for Electrical Applications?
The electrical industry demands components that can withstand extreme temperatures, resist chemicals, and maintain their physical properties over time. Polyurethane shines as a superior choice for electrical applications. Its outstanding insulation capabilities make it an excellent material for insulating components, protecting against electrical leaks, and ensuring reliable performance.
Unlike traditional molding methods, polyurethane molding offers the flexibility to create complex shapes, sharp corners, and intricate designs. This level of customization is crucial in the electrical industry, where every component must fit precisely and function flawlessly within the larger system.
How Does the Polyurethane Molding Process Work?
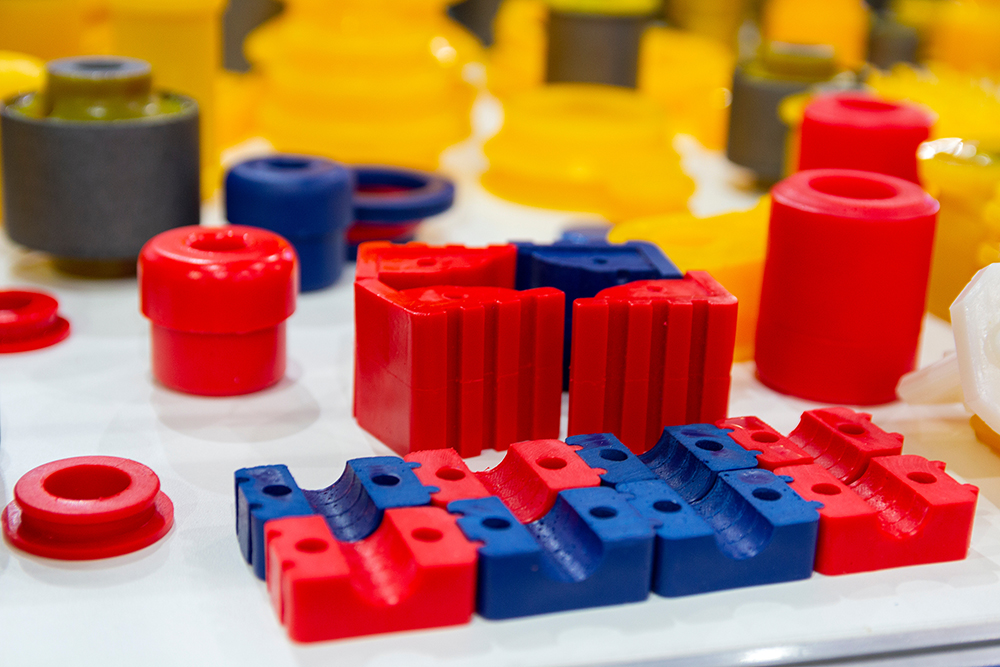
The process of polyurethane molding—sometimes called cast urethane molding—involves a series of steps that transform liquid polyurethane into a solid, durable component. It begins with creating a primary model or pattern, which serves as a template for producing multiple identical parts. This creation can be achieved through techniques such as CNC machining or 3D printing.
Once the primary model is prepared, a mold is created around it using materials like metal or carbon steel. The mold is designed to accommodate the desired shape and features of the final product. Before pouring the liquid polyurethane into the mold, a mold release agent, like our E236 Urethane Mold Release, must be used to help fully release the part. The mold may also be preheated to ensure proper flow and minimize air bubbles.
During the casting process, two liquid components of polyurethane—a resin and a curative—are mixed together. This chemical reaction initiates an exothermic process, causing the mixture to heat up and solidify. The heated mold helps accelerate this process, resulting in a shorter production cycle.
After the polyurethane has fully cured and solidified, the mold is opened, and the finished product is removed. The part may undergo additional post-processing steps, such as trimming excess material or applying surface finishes, to achieve the desired final appearance and specifications.
Stoner Molding Solutions offers a range of products and expertise to support the polyurethane molding process. From mold release agents to mold cleaners, our solutions are specifically formulated to enhance efficiency and quality throughout the entire molding process.
What Impact Has Polyurethane Made in the Electrical Industry?
The impact of cast urethane molding on the electrical industry has been transformative. By leveraging the unique properties of polyurethane, manufacturers can produce components that meet the industry's stringent requirements. From insulating materials that provide reliable electrical insulation to protective covers that safeguard sensitive electronics, polyurethane has proven its worth in numerous electrical applications.
One significant advantage of polyurethane is its ability to withstand extreme temperatures, making it ideal for applications where heat dissipation is crucial. Whether it's high-temperature environments or electronic devices that generate heat, polyurethane can maintain its physical properties without compromising performance.
Additionally, polyurethane offers excellent resistance to chemicals, ensuring the longevity and reliability of electrical components even in harsh operating conditions. This resistance extends to factors such as moisture, solvents, oils, and other substances commonly encountered in electrical applications.
The durability of polyurethane also contributes to its impact on the electrical industry. It provides a long service life and can withstand mechanical stresses, ensuring the integrity of components over an extended period. This durability reduces the need for frequent replacements, minimizing downtime and increasing cost-effectiveness for manufacturers.
Are There Any Future Trends to Watch for in the Polyurethane and Electrical Industries?
As technology continues to advance, the polyurethane and electrical industries are poised for exciting developments. Some trends to keep an eye on include the following:
MIniaturization
One trend to watch is the increasing demand for miniaturization in electrical components. As devices become smaller and more compact, polyurethane will play a crucial role in meeting the evolving needs of these industries. The versatility and customizable nature of polyurethane molding make it an ideal solution for creating intricate and precise components that meet the demands of miniaturization.
Sustainability
Another trend to keep an eye on is the growing emphasis on sustainable and environmentally friendly practices. With the increasing focus on reducing carbon footprints and achieving sustainability goals, manufacturers seek materials and processes aligning with these objectives. Polyurethane, with its potential for recyclability and energy efficiency, is well-positioned to contribute to future green initiatives.
Technology Advancements
Furthermore, technological advancements are driving innovation in the polyurethane and electrical industries. Integrating smart technology and Internet of Things (IoT) capabilities is revolutionizing how electrical components operate and interact with their environment. Polyurethane's unique properties, such as its durability and resistance to extreme temperatures, make it an ideal material for these advanced applications.
New Formulations and Additives
The continued exploration of new formulations and additives for polyurethane molding will further enhance its performance and expand its potential uses in the electrical industry. Whether it's improving flame retardancy, enhancing conductivity, or increasing thermal insulation properties, research and development efforts are continuously pushing the boundaries of what polyurethane can achieve.
As the world becomes increasingly interconnected and reliant on advanced electrical systems, the demand for high-quality polyurethane components will only continue to grow. By staying informed and embracing these future trends, manufacturers can leverage the benefits of polyurethane molding to create innovative, reliable, and sustainable solutions for the electrical industry.
Need Help Optimizing Your Polyurethane Molding Process? Contact Us!
If you're facing challenges in the electrical industry, such as finding reliable and high-quality components that can withstand extreme conditions, it's time to take action. The impact of polyurethane molding on the electrical industry is a game-changer. Its exceptional properties and versatility make it the ideal solution for your needs. As you've learned in this blog post, polyurethane offers outstanding insulation, durability, and resistance to chemicals, ensuring reliable performance in even the harshest environments.
With our expertise in industrial molding solutions and a focus on top-quality mold release agents, we are ready to help you overcome your challenges. With high-quality mold release agents, cleaners, rust preventatives, and lubricants, we can help you mold more parts in less time so that you can keep up with the latest trends.
Get started on your journey to efficiency and reliability. Reach out to Stoner Molding Solutions and take control of your polyurethane molding process. Together, we can turn your frustrations into triumphs and pave the way for a brighter future in the electrical industry.
Resources: