5 Most Frequently Asked Questions About Compression Molding Composites
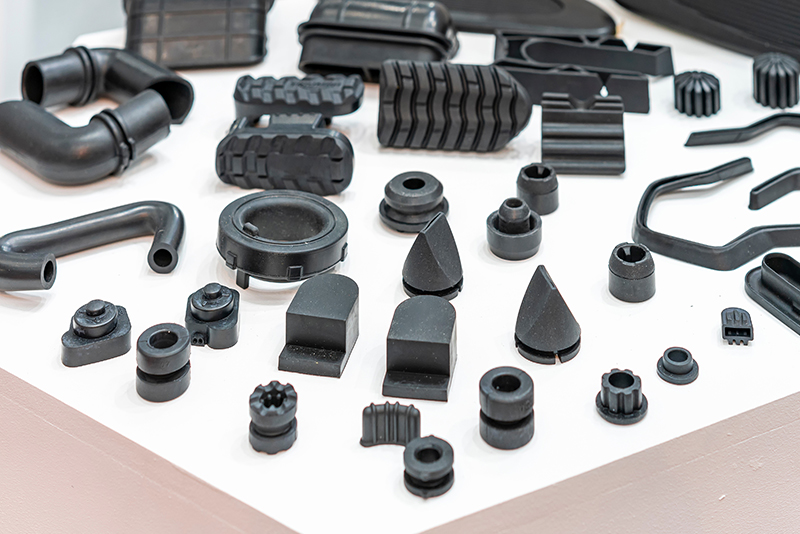
Do you know the epoxy resin's chemical composition off the top of your head? Or the activation energy of common catalysts? The mass production of composites is a rigorous and competitive field that requires you to stay well-informed to stay ahead.
Whether old hat or new blood, you should make every effort to remain well-informed and ahead of the curve of your field. Some of the most asked questions have been compiled and answered below to start a guide on the most must-have knowledge in the composite molding industry.
1. What is the Difference Between Injection and Compression Molding?
While both types of molding are heavily used in industrial factories today, both injection and compression molding have very different uses and practices. Injection molding forcefully injects material into a mold, which is then split to de-mold the end product. This process can result in higher-detail pieces and uses different materials.
Compression molding, on the other hand, places material on one half of a mold and then uses a mixture of heat and high pressure to secure the other half of the mold to its mate. This a slightly slower process, and has less detail in the end product. However, compression molding is much more flexible in terms of materials used, since the part doesn’t have to undergo high-force injection.
2. What Types of Composite Materials Are Used in Compression Molding?
Composite materials are typically polymer resins impregnated with woven or chopped fibers. Like bronze is stronger than copper or tin, advanced composites are often much stronger than composite components. Not all materials can be combined effectively, but the most popular polymers and fibers are:
Body Materials
- Polyester Resins
- Epoxy Resin
- Vinyl Ester
- Phenolic Resin
Reinforcements
- Carbon Fiber
- Glass Fiber
- Kevlar
Each of these materials represents a unique benefit to the end composite material. Carbon fiber-reinforced composites are often used in the aeronautics industry for their strength and low weight, while glass fibers are common materials in nautical body pieces.
The bulk material is layered with fiber content, providing tensile strength when forming composite molded parts. This process works much like how rebar is added to concrete. The fiber orientation and fiber volume will vary depending on need.
3. What Is the Compression Molding Process?
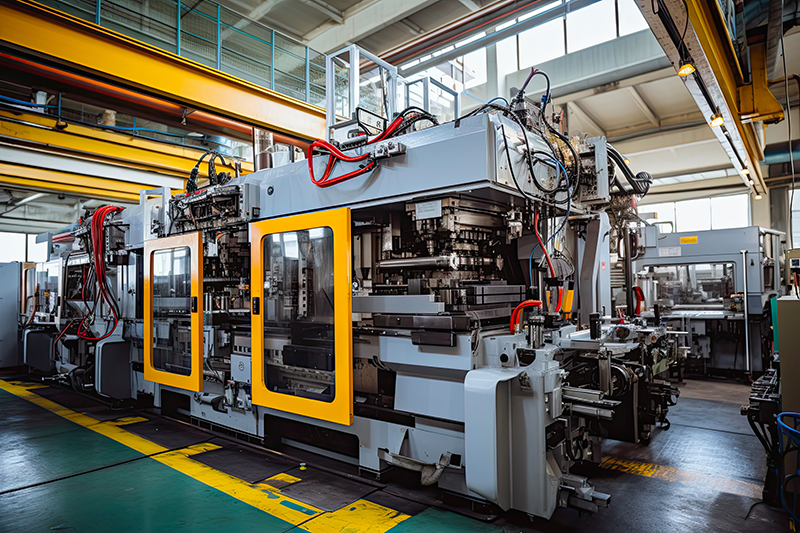
Many manufacturing steps go into the process of compression molding composites to maintain high output and quality. The various stages of the process work together to provide shape, strength, and appearance to the molded part.
Prepare the Charge
Excessive material is wasteful, so careful measuring ensures all materials used won't excessively overflow the mold. Pretreatments such as mold sealant or release are applied to the mold cavity.
Load the Mold
The cavity of the mold is filled with the material or mixture. The fiber compound can be layered in the mold, or chopped fibers can be mixed with the bulk material.
Apply Heat and Pressure
Pressure and heat are used to fill the mold cavity. High heat and constant temperature ensure the material will soften and flow smoothly as it is compressed. Mold lubricants can help smooth the movements of the mold.
Cure the Piece
Thermoplastics need to be cooled to solidify completely. Catalysts promote the curing process and ensure high stiffness for rubbers and thermoplastics.
Release the Piece
After the curing reaction and cooling, the mold is opened, and the piece is released. This step can be automated for complex shapes and high-volume production and improved via mold-release products.
Trim and De-Flash
Flashing is a little bit of excess material that leaks from a mold. This overflow ensures that the mold is filled, and the piece is whole. Any excess flashing is removed after the part is released.
Clean the Mold
After ejection, the mold is cleaned and cleared of any spare material that might interfere with the subsequent use. Release agents are applied to prevent future sticking.
This process can be tailored to the needs of mold material and more unique pieces. Woven fabrics and more structured fiber layers might require more care during loading, and overly complex geometries might require more heat and pressure for flow patterns to fill the mold.
4. What Industries Use Composite Compression Molding?
Composite molding presents many benefits to the parts it produces. Because of the strength and durability of composite structures, several industries have leaped at the chance to have a lightweight and durable creation. Every industry has its favored materials and products tailored to its needs.
Aerospace
Low weight-to-strength ratio and high mechanical performance have provided aerospace industry experts with a fantastic material to work with.
Automotive
The mechanical properties of composites have improved vehicle safety without sacrificing performance or safety, making it an ideal material.
Medical
Composite materials can be made to be X-ray transparent for diagnostic beds and cases, and prosthetics can be lightweight and durable.
Consumer Products
Low manufacturing costs are desirable for mass-market products, especially when combined with high-volume manufacturing rates.
The remarkable flexibility of the molding processes can provide unique benefits to nearly any industry if the part designer has the creativity and vision to follow up. Composite part cost, strength, and durability will continue to improve as more advancements are made in molding materials and technology.
5. How Should Compression Molded Parts Be Designed?
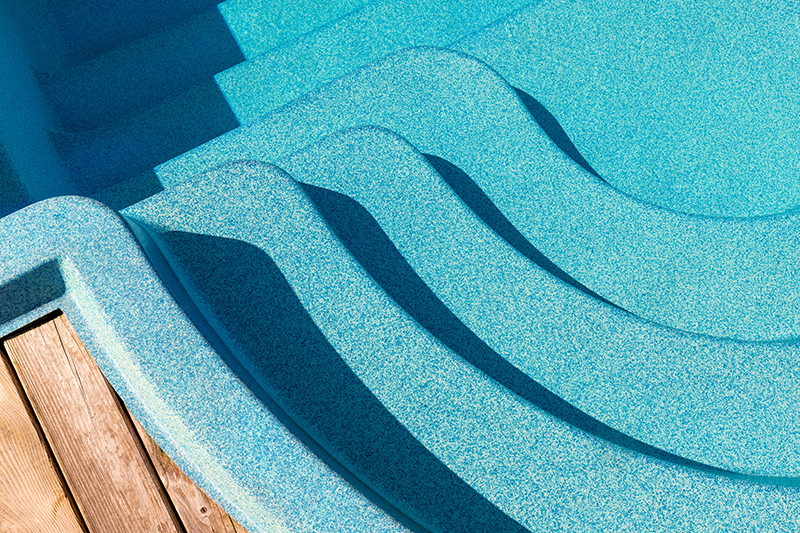
The molded part design needs to consider the production process. Poor reproducibility is something that needs to be avoided to ensure a successful mold. But when designing around the process, some specific considerations can be made to help.
- Thin walls - When the chemical reactions of the final cure occur, thicker areas can take longer to finish. Keeping thinner piece walls will help ensure faster production.
- Avoid Unnecessary Undercuts - Undercuts and geometric complexity are not reasons to avoid a mold. Still, they should be considered negatives because of the difficulty they can cause during de-molding.
- Smooth Shapes Are Best - Compression molding composites does not lend itself to sharp edges and hard corners. The smooth lines and edges are part of why vehicle manufacturers have readily employed compression molding.
- Hide the Parting Line - This is slightly more of an aesthetic concern, but where the mold separates and opens up for filling and de-molding, it should be hidden along edges and curves.
Designing a compression molded composite piece requires knowledge of material needs, structural needs, mechanical properties, and the process of molding itself. Composite parts are highly customizable and viable in many use cases.
Come to Stoner Molding for Any of Your Compression Molding Composite Questions.
The molding industry demands knowledge of advanced composites and intricate processes for handling them. You don't want to risk damage to your mold, money loss from incomplete parts, or complaints from poorly designed pieces. You want to provide your customers with the absolute best possible product. These questions and answers should help you on the path to industry stardom.
When you continue developing and producing compression molding composites, look to Stoner Molding Solutions for ways to get the most from your molds. Sealers, releases, lubricants, and cleaners are all products that can provide you with marked benefits to your process. If you have any questions about products or the molding industry, contact the company that supports dozens of industry leaders.